WoodWise
Use Cases and Scenarios
WoodWise can help in many different ways. Explore the different use cases and functionalities that helped these clients improve their production processes.
Story 1: How WoodWise drives small shops
How WoodWise Helped a Small Woodshop Overcome Job Confusion
Key Results
​​
​
Story:
The owner of a small woodshop, was passionate about crafting custom furniture pieces. The shop was a one-man operation, and while he was skilled in woodworking, managing multiple projects simultaneously proved challenging. He often found himself in a bind when parts for different jobs got mixed up. The resulting confusion led to delays, wasted materials, and frustrated customers.
One day, he learned about WoodWise, a state-of-the-art Operational Technology (OT) platform specifically designed for woodworking businesses. Intrigued by the promise of better organization and efficiency, he decided to give it a try.
After implementing WoodWise, Tom quickly noticed several improvements in his workflow:
-
Job Tracking and Organization: WoodWise provided the owner with an intuitive job tracking system. Each job was assigned a unique identifier, and he could easily tag and categorize each piece of wood according to its job. This eliminated the confusion of mixing up parts and ensured that every piece was correctly matched to its project.
-
Real-Time Monitoring: With the platform's real-time monitoring capabilities, Ownership could keep track of the progress of each job on a centralized dashboard. He could see at a glance which tasks were completed, which were in progress, and which needed attention. This visibility helped him stay on top of his workload and prioritize tasks more effectively.
-
Automation and Alerts: WoodWise's automation features allowed ownershipp to set up alerts for key milestones and deadlines. The system notified him when it was time to start a new phase of a project or when a task was nearing its deadline. This proactive approach helped manage time better and avoid missing important deadlines.
-
Quality Control: WoodWise provided tools for quality control, allowing him to document each step of the production process and ensure that every piece met his high standards. This consistency in quality further delighted his customers and built his reputation as a reliable craftsman.
With WoodWise, helped transform the shop from a chaotic, one-man operation into a well-organized, efficient business. The business no longer worried about mixing up parts or missing deadlines. Instead, the owner could focus on what he loved most: creating beautiful, custom furniture pieces for his satisfied customers.
This story is a testament to how even a small woodshop can benefit from the advanced features of an OT platform like WoodWise. By improving organization, tracking, and efficiency, WoodWise empowered this shop to take his business to the next level, delighting his customers and ensuring long-term success.
How does it work?
WoodWise includes a Google Sheets/Microsoft Excel upload for part and job tracking. For this use case, there was no labeling required. The client only wanted to track jobs digitally and manually control parts flows as pieces were cut and moved to the next station. Using a touch screen to indicate parts flow, the client could easily determine percentage of job complete and give customers a clearer picture on lead time. The next day, the client could easily pick up where they left off and continue seamlessly.
Increased customer satisfaction with faster shipping times and complete orders (no missing parts).
Reduced rework and lost parts through part tracking per job allowing client to cut more parts per job.
Simple parts list import to track jobs and parts using the WoodWise dashboard implementation.
Story 2: How WoodWise transforms medium-sized shops
How WoodWise Transformed a Medium-Sized Woodworking Company
​
Key Results
​
​
​​
​
​​​
Story:
​A medium-sized woodworking company specializing in custom cabinetry and furniture had invested in a CAD/CAM solution to design and program their CNC machines, but once the designs left the office, chaos reigned on the shop floor. The production area was plagued by missing parts, frequent rework, and an overall lack of organization, causing delays and increased costs.
​
The production manager, knew they needed a solution to bridge the gap between their office operations and the physical production process. That’s when they discovered WoodWise.
​
After implementing WoodWise, the company experienced a remarkable transformation:
​
-
Integrated Part Tracking: WoodWise seamlessly integrated with their existing CAD/CAM solution, allowing for automatic generation of part tracking data. Each part produced on the CNC machines was tagged with a unique identifier linked back to the original digital design. This ensured that every piece could be tracked throughout the production process.
-
Real-Time Production Monitoring: The platform provided real-time monitoring of the shop floor. The team could see the status of each job, track the movement of parts, and identify any delays or issues immediately. This visibility allowed them to address problems proactively, reducing downtime and improving overall efficiency​​.
-
Enhanced Workflow Organization: WoodWise offered tools to organize the workflow on the shop floor. Jobs were prioritized, and workstations were assigned tasks in a logical sequence. This reduced confusion and ensured that all parts were processed in the correct order, minimizing the risk of missing parts and rework​​.
-
Inventory and Resource Management: WoodWise also helped manage inventory and resources more effectively. Materials were tracked from the moment they entered the shop until the final product was shipped out. This level of oversight ensured that they always had the necessary materials on hand and could quickly reorder when stocks were low​.
-
Enhanced Communication and Collaboration: With WoodWise, communication between the office and the shop floor improved significantly. Design changes made in the CAD/CAM system were instantly updated in the production tracking system, ensuring everyone was always working with the most current information. This reduced errors and improved collaboration across the team.
Within a few months of implementing WoodWise, the company saw a dramatic reduction in missing parts and rework. The shop floor was organized and efficient, and production ran smoothly. The team could now focus on meeting customer deadlines and maintaining high-quality standards, rather than constantly putting out fires.
The implementation of WoodWise not only improved day-to-day operations but also positioned the company as a leader in the custom woodworking industry. By leveraging the power of an OT platform, they could deliver top-notch products to their clients, on time and within budget, driving growth and success for the company.
Enabled automatic part tracking by integrating with CAD/CAM, ensuring accurate tracking throughout production.
Real-time monitoring of the shop floor, quickly identifying and resolving issues to improve efficiency.
Organized workflows, prioritizing jobs and sequencing tasks to reduce confusion and rework.
Story 3: How WoodWise bridged the gap from production to office
How WoodWise Resolved Production Deficiencies and Improved Decision-Making
​
Key Results
​
​
​​
​​​​​
​​
Story:
​
A medium-sized woodworking company, prided itself on crafting high-quality custom wood products. However, they were facing significant production deficiencies. Despite having a CAD/CAM system in place, the shop floor was disorganized, parts were frequently missing, and rework was common. Moreover, the lack of data flow from the shop floor to the office made it difficult for the management to make informed decisions on capacity planning and to coach their production team effectively. The company tried using Google Sheets, but it was a manual process and updates were infrequent at best.
​
The operations manager, knew they needed a comprehensive solution that could streamline production and provide real-time data to the office. The company discovered WoodWise, an OT platform designed to integrate seamlessly with existing systems and improve overall operational efficiency.
​
After implementing WoodWise, the company experienced a remarkable transformation:
​
-
Integrated Part Tracking and Real-Time Monitoring: WoodWise integrated with their CAD/CAM system, enabling automatic part tracking and real-time monitoring of the shop floor. Each part was tagged with a unique identifier, and production and management could track every piece throughout the production process. This integration drastically reduced the instances of missing parts and rework, as the system provided clear visibility and control over the workflow​ on the production floor as well as in the office with job and parts feedback.
-
Data-Driven Decision Making and Capacity Planning: WoodWise collected and reported real-time production data back to the office. Management could access detailed reports and dashboards, which provided insights into production rates, machine utilization, and bottlenecks. This data was crucial for effective capacity planning, allowing the company to optimize resource allocation and ensure that production schedules were met. The ability to analyze historical data also helped the management make informed strategic decisions and even decide on a performance objective for production to boost productivity​.
-
Coaching and Performance Improvement: The real-time data and detailed reports generated by WoodWise were used as coaching tools for the production team. The team could identify areas where individual operators or processes were underperforming and provide targeted coaching to improve efficiency. The transparency and accountability brought by the system motivated the team to strive for higher standards and continuously improve their performance​.
In a matter of months, the company saw a dramatic reduction in production deficiencies. The shop floor became more organized, the instances of missing parts and rework were minimized, and production efficiency improved significantly. The management team was empowered with real-time data and insights, enabling them to make informed decisions and effectively coach their production team.
WoodWise not only resolved the immediate issues but also set the foundation for continuous improvement and growth. By bridging the gap between the shop floor and the office, WoodWise optimized their operations, enhance team performance, and achieve long-term success in the competitive woodworking industry.
Reduced missing parts and rework by providing automatic part tracking and real-time monitoring
Improved capacity planning and strategic decisions through real-time production data and insights
Enabled targeted performance improvements by using real-time data and reports for effective team coaching
Story 4: WoodWise goes high tech to automate advanced feedback
How WoodWise Transformed a Highly Automated Woodworking Company
​
Key Results
​
​
​​
​​​​​
​​
Story:
​
A larger woodworking company with more advanced levels of automation, including machinery with PLC systems, parts conveyors and machinery lines with integrated systems, was experiencing rapid growth. They had invested in advanced CAD/CAM systems, optimization, and nesting solutions for inventory management. However, as their business expanded and more employees joined, they faced significant challenges in job and parts tracking. Parts were often misplaced, broken pieces forgotten in the rework process, and paper job travelers were regularly lost or mixed up, causing costly delays and errors.
​
The manufacturing operations manager, knew they needed a solution that could automate part data feedback from machinery without relying on manual scanning. In addition, they could not find skilled labor to join the team. They needed a solution that was easy to implement and help provide on-the-job training to new colleagues to keep production moving and reduce disruption of the production process.
After researching various options and decided to implement WoodWise, an OT platform designed to seamlessly integrate with their existing systems and streamline their operations.
​
Once WoodWise was up and running, The company experienced a remarkable transformation:
​
-
Automated Part Data Feedback: WoodWise integrated with their machinery to automatically capture and report part data. Each part produced was instantly logged into the system without the need for manual scanning. This automation reduced errors and ensured accurate tracking of every piece throughout the production process.
-
Streamlined Job Tracking: The platform replaced the outdated paper job travelers with digital job tracking. Jobs were tracked in real-time, and all relevant information was accessible on centralized dashboards. This eliminated the problem of misplaced or mixed-up paperwork, ensuring that all job details were accurate and up-to-date.
-
Efficient Rework Management: WoodWise provided a robust system for managing rework. Broken or defective pieces were flagged and tracked through the rework process, ensuring they were not forgotten or overlooked. This improved overall quality control and reduced the time and cost associated with rework​.
-
Enhanced Communication and Collaboration: With WoodWise, communication between departments improved significantly. Information flowed seamlessly from the shop floor to the office, enabling better coordination and decision-making. The platform also provided tools for assigning tasks and tracking their progress, enhancing collaboration across teams.
-
Scalability and Growth Management: WoodWise's scalability allowed the company to continue growing without being hindered by operational inefficiencies. The platform's automated systems and real-time data tracking kept pace with the company's expansion, ensuring that new employees and processes were integrated smoothly and efficiently​.
As a result of implementing WoodWise, the company saw a dramatic reduction in production errors and delays. The shop floor became more organized, and the overall efficiency of their operations improved. The team was empowered with real-time data and insights, enabling them to make informed decisions and manage the company's rapid growth effectively.
​
WoodWise not only resolved the immediate challenges but also positioned the company for continued success. By automating part data feedback and streamlining job tracking, WoodWise helped maintain high standards of quality and efficiency, ensuring they could meet increasing customer demands and thrive in the competitive woodworking industry.
Automated the capture and reporting of part data directly from machinery, eliminating manual errors and ensuring accurate tracking
Replaced paper job travelers with digital tracking, preventing lost or mixed-up paperwork and maintaining accurate, up-to-date job details
Flagged and tracked defective pieces through the rework process, improving quality control and reducing rework time and costs
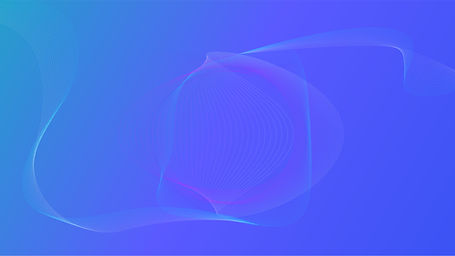